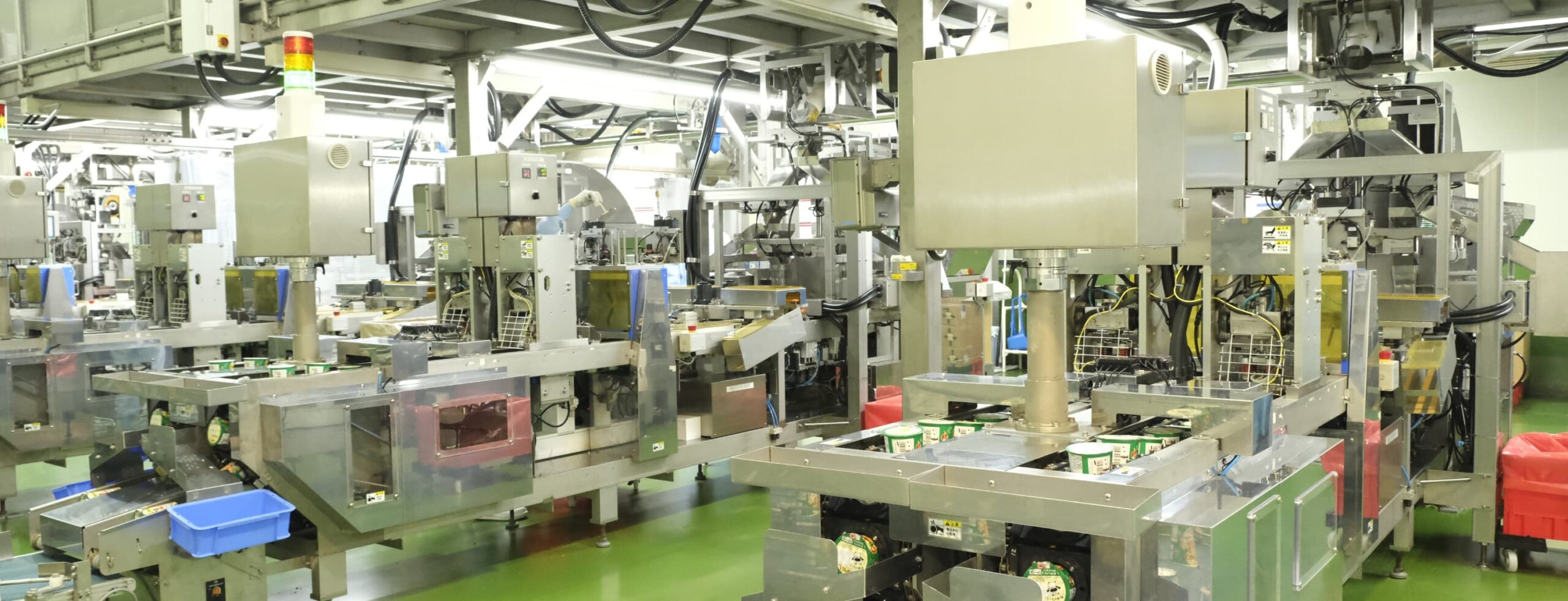
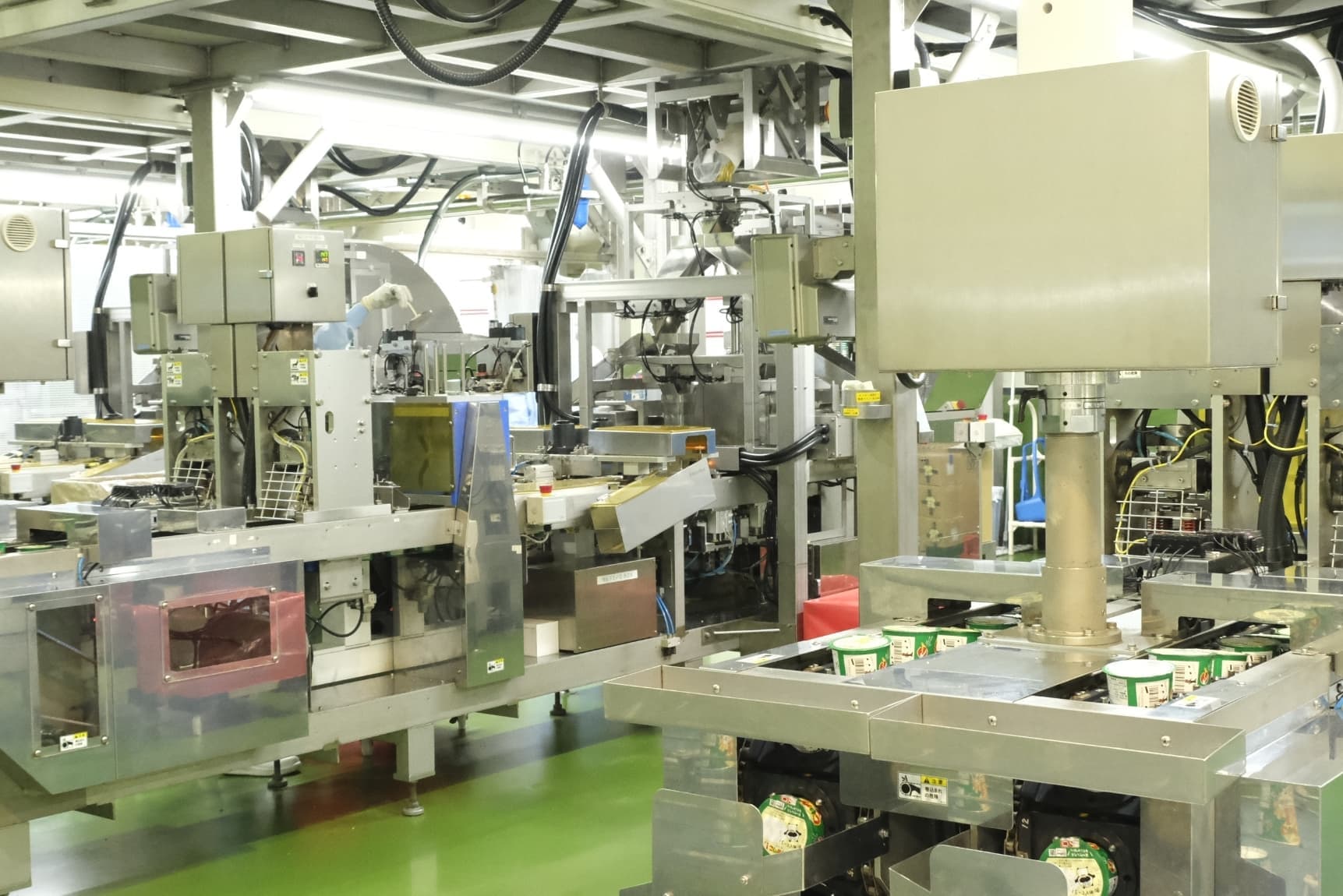
プロジェクトストーリー
新工場建設。
作業員の事を考えたレイアウト作り
このプロジェクトのメンバー
-
K.Nishibu
新工場建設事業の始動
-
当時、弊社はカルビー株式会社の協力工場としてポテトチップスの製造を行っていました。しかし、じゃがりこの需要が増加しているという市場の動向を受けて、じゃがりこ事業に参入することが検討されました。その話が持ち上がってから約1年半後、新工場の建設が本格的に決定しました。
今までの経験と作業者目線を活かした設備設計
-
新工場建設のプロジェクトにおいて、私は特に生産設備と付帯設備の構築に関わりました。生産設備については、詳細な仕様の確認が主な役割でした。一方、階段、手すり、手洗い場などの付帯設備については、これまでの経験や作業者の視点を活かし、設計者との連日の打ち合わせを通じて、レイアウトや設備架台などの細部について具体的に設計しました。
作業者の負担を軽くするための念入りな調査
作業者の負担を
軽くするための念入りな調査
現代の食品工場では、管理項目に対して作業者の負担を軽減し、将来的にも設置場所を疑問視されないような設計やレイアウトが求められるため、細部まで入念に考慮する必要がありました。そのため、帯広や京都などのモデルとなる工場を研修先として訪れ、作業内容を把握し、あらゆる場面を想定して設計を進めました。
特に重要視したのは、機械メンテナンスのしやすさと作業後の管理です。自動化された工場では、機械の管理が主要な要素となります。他の工場で修理作業に苦労するという話を聞いたこともあり、修理しやすい配置を心掛けました。また、製造ラインの上方に照明などを設置しすぎると、作業後の点検や管理に時間がかかってしまうため、必要最低限かつ作業に支障が出ないバランスを考慮しました。
実際に機械が設置されると、予想よりもスペースが狭かったり、希望した設計がうまく機能しないこともありました。しかし、工事業者の方々に協力していただき、最終的には作業しやすい工場を実現することができました。
新工場が動き出してからも一苦労
-
工場が完成し、設備を初めて稼働させる際には予測できないトラブルが起こる可能性もあります。そのため、新工場が稼働してから約1カ月間は、当時の部長と私が交代で現場に常駐しました。
また、新しい工場であっても、適切な管理が行われなければ老朽化が進んでしまいます。そのため、私たちは整理・整頓・清掃・清潔・しつけを意味する5S活動に取り組み、細かいルールを設けて日常的に実践するよう意識づけました。これにより、5Sが当たり前の行動として浸透し、効率的な工場運営と維持管理が実現できました。
今回のプロジェクトを通して得られたものとは?
今回のプロジェクトを
通して得られたものとは?
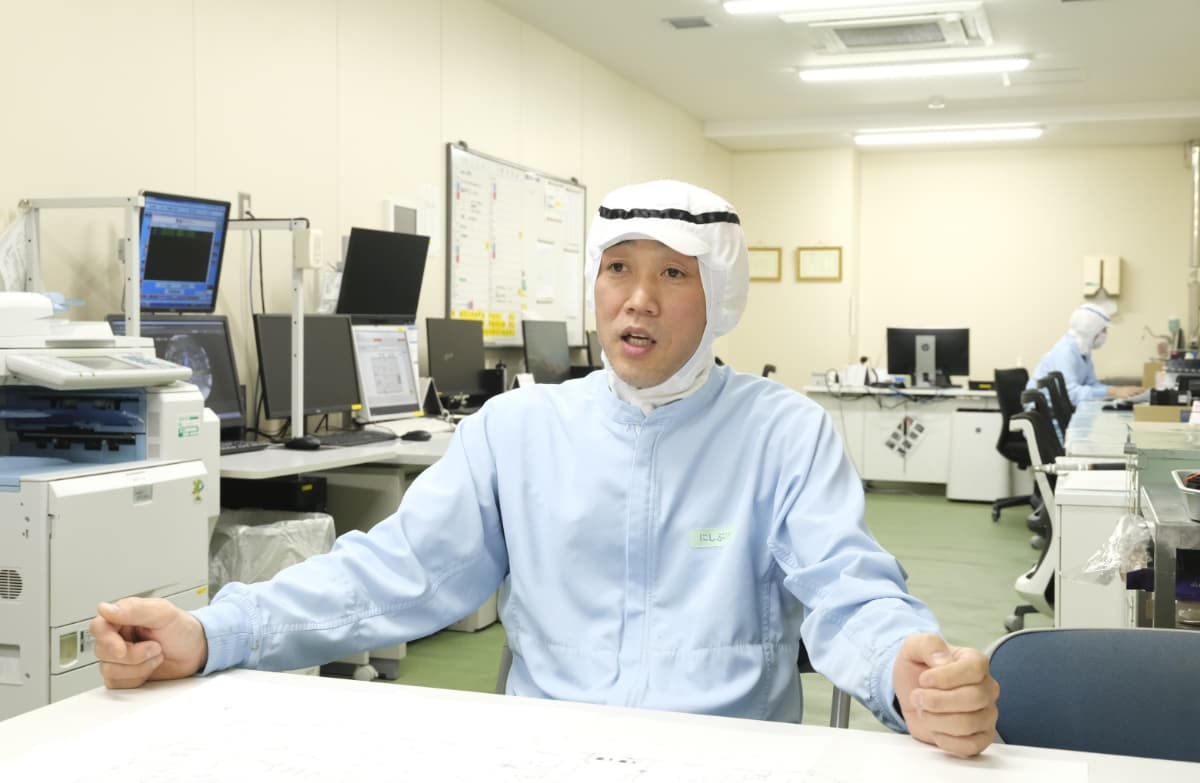
スナック食品部のメンバーは今でも5S活動の重要性を認識しており、工場の監査でも全国一と称されるほどの評価を得ています。工場の5S管理は約20年前から始まっており、当初から関わってきたメンバーが主体となり、新規メンバーにしっかりと継承されています。今後もこのようなプロジェクトに関わる機会があれば、現場の中堅社員にぜひ参加してもらいたいと思っています。